KMotion, KMotionCNC, and our Feature-rich Libraries
Dynomotion's current software package comprises three major components:
- KMotion.exe (pronounced 'commotion'), which is used to configure settings in KFLOP/Kogna, initialize axes, and to write C programs to control your system.
- KMotionCNC, which is our CNC application that has a GUI (Graphical User Interface) and is used to control systems based on G-Code. Alternatively, we have a Mach3 plugin so our boards can be used with the Mach3 CNC application.
- The KMotion libraries that form the heart of the other two software components as well as user-created or third-party applications.
KMotion.exe
KMotion.exe (or KMotion - pronounced like 'commotion') is the main program that is used to configure settings in KFLOP/Kogna, initialize axes, and to write C programs to configure and setup KFLOP/Kogna to control your system.
KMotionCNC
KMotionCNC is our free CNC program used as a graphical user interface to your KFLOP/Kogna-enabled machine tool. A Custom Screen Editor is supported. KMotionCNC has all of the functionality you need to run a machine of up to 8 axes, in addition to spindle control, jog buttons, tool setup features such as tool width compensation for up to 100 tools, pre-loaded tool types, trajectory planner parameter adjustments, user-defined M-Codes, G-Code capabilities, and a G-Code viewer. In addition RTCP and Kinematics are supported. Rigid tapping and single point threading as well. Geo-correction routines can be used to drastically improve the accuracy of your system.
KMotionCNC depends on some simple setup and initialization of your system that can be completed one time in KMotion.exe and then called from KMotionCNC thereafter.
More information about our free KMotionCNC software
Other Options - Mach3 Plugin
Besides writing your own software or using .NET compatible third-party software to tie into our libraries, you have the option to use a popular CNC application called Mach3 much as you would KMotionCNC.
Significant Flexibility
Throughout our product line our goal is to provide extreme flexibility and this is reflected in our software. At every turn, in every choice we had to make, we chose to provide the user with the option that allowed for more flexibility. After spending the time to learn how to use them you will understand just how powerful are our boards and software. So with a little up front investment, you can have years of tailored motion control.
Free Download
Our latest software is available for free at the link below.
Download here: http://dynomotion.com/Software/Download.html
KMotion Software Libraries
Dynomotion's KMotion software libraries contains the following components:
- A Dynomotion-developed Trajectory Planner
- A Dynomotion-developed Coordinated Motion Library
- A G-Code interpreter
- Kinematics Layer with Geo-Correction
- .NET interface
The KMotion libraries are powerful in that they do all of the difficult computational and coordinated tasks for the user. You can create your own software to make use of the libraries directly, or through the .NET framework, or use third-party software that already makes use of the .NET framework such as National Instruments' LabVIEW.
KMotion Software Breakdown:
Mode |
Parameter |
Specification |
User Programs |
Language
Number concurrent
Stand alone mode |
C
7
Yes |
Host Requirements |
OS
Interface |
Windows™ 7 through 11; 32 and 64 bit
KFLOP: USB 2.0 - Kogna: Ethernet |
Interface Library |
Multi-Thread
Multi-Process
Multi-Board
MS Windows™ VC++
MS Windows™ VB
C#
.NET |
Yes
Yes
Yes
Supported
Supported
Supported
Supported |
C Compiler |
TCC67 |
Included |
G Code |
Interpreter |
Included |
Script Language |
ASCII Commands |
Included |
Trajectory Planner |
Coordinated Motion |
KFLOP: 8 Axis - Kogna: 16 Axis |
Exectuive Application |
Configuration
Tuning
User Programs
G Code
Command Console
Status Display |
Upload/Download/Save/Load Motor Config Move/Step Response, Bode Plot, Calc Filters
Integrated IDE - Edit/Compile/Download/Exec
Integrated
ASCII Command Entry - Log Console
Axis/Analog/Digital |
Please view our on-line documentation for full details
Some of KMotion's Configuration, Servo Tuning, Status, Programming Screen Examples:


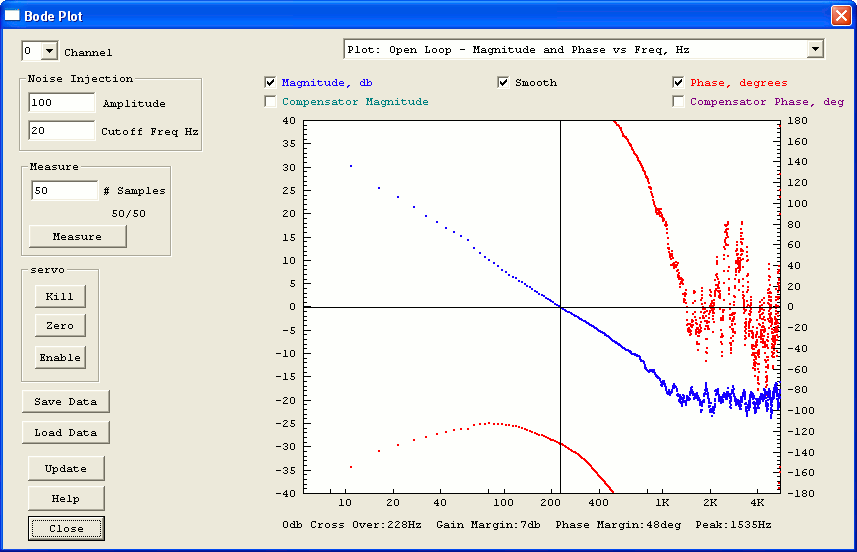
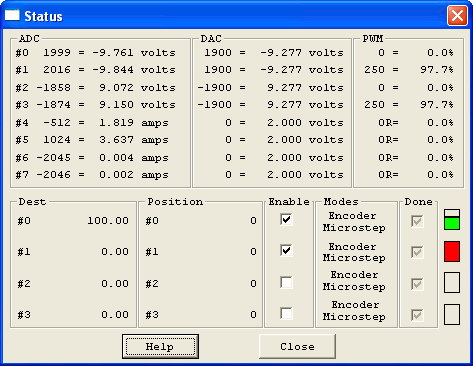

Copyright © Dynomotion, Inc.
|