Page 1 of 2
need some AMC analog amplifier Gain tuning help
Posted: Thu Mar 07, 2024 5:00 pm
by turbothis
so i got my DC servo spindle running perfect by dialing in these settings
loop gain full CCW
current limit full CW
ref in gain full CW
and adjusted the offset to find the sweet spot where the servo does not run off in either direction
great!
now i try this on my Z axis servo with 2 other identical model drives and for the life of me cant get any kind of useful motion and tune out of them.
either the servo is running away in a direction or when i get it still the +/- input has no effect on output
i have a scope if that could help me figure out why the same servo and model drives would have zero in common
any help on this?
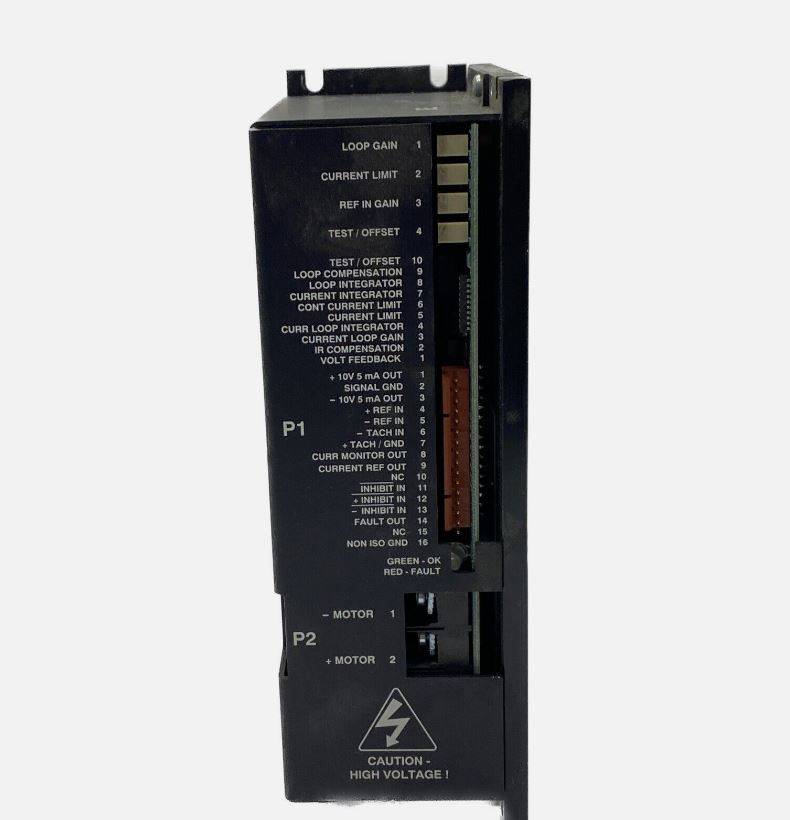
Re: need some AMC analog amplifier Gain tuning help
Posted: Thu Mar 07, 2024 6:14 pm
by TomKerekes
What do you do to "get it still"?
Do you have a tachometer?
Re: need some AMC analog amplifier Gain tuning help
Posted: Thu Mar 07, 2024 6:26 pm
by turbothis
the spindle drive was easy enough to adjust the offset to get it still
the Z axis will not show any change with full offset range applied
i have a laser tach reader? i dont have any tach input to the drive though
these are running in current mode
Re: need some AMC analog amplifier Gain tuning help
Posted: Thu Mar 07, 2024 6:33 pm
by turbothis
its interesting that the current limit pot will reverse the direction of the servo while spinning about one turn away from full adjustment
this is still at full rpm (2300)
Re: need some AMC analog amplifier Gain tuning help
Posted: Thu Mar 07, 2024 7:01 pm
by TomKerekes
Do you have the switches set the same?
You might connect the Tach + and - inputs together and to TACH GND so there is zero tach input.
Also Ref + and - inputs together and to Signal GND so there is no command input.
The offset Pot should then operate as a current command input. Note because it is operating in current (acceleration) mode It can be very difficult or impossible to "sit still" The smallest offset or noise can cause the motor to gradually accelerate to a high speed. Note in normal closed loop operation this is a non-issue because as soon as the position begins to drift away the servo will make a correction to move it back. But open loop the acceleration will continue. Even though it may not ever "sit still" the direction of acceleration should be controllable by the offset and should be very minimal.
Re: need some AMC analog amplifier Gain tuning help
Posted: Fri Mar 08, 2024 12:37 am
by turbothis
dam, it showed no difference with the tach and +/- signal grounded
Re: need some AMC analog amplifier Gain tuning help
Posted: Fri Mar 08, 2024 12:41 am
by turbothis
i believe that the controller can settle the rotating , but
if the following error disables that axis, run on is back until the E stop disables the drive. right?
it worked perfect before too though
i think lighting struck my house at some point
Re: need some AMC analog amplifier Gain tuning help
Posted: Fri Mar 08, 2024 1:18 am
by TomKerekes
Re: need some AMC analog amplifier Gain tuning help
Posted: Fri Mar 08, 2024 6:41 pm
by turbothis
ya i got that info pretty good
i ordered up another drive for if this does not play ball again
i have to turn the current limit up high enough the servo has lots of power to run away
i figure i will run a test....
1 clamp servo shaft to something immovable
2 INIT axis to come online and hold position
3 enable drive
4 check servo in question
5 unclamp if looks safe... ish
6 command some slow movements and see how dangerous this is all working out to be. lol
Re: need some AMC analog amplifier Gain tuning help
Posted: Fri Mar 08, 2024 7:41 pm
by TomKerekes
I'd test the drive first before trying more complicated things.
Commanding small DAC voltages should command the motor current (torque) proportionally and both + and -. If this doesn't work moving forward doesn't make sense. Current Limit should have no effect unless the command current is greater than the limit.
Clamping the shaft while enabling the servo can cause problems depending on servo parameters. If there is I gain even with a tiny error the servo will try harder and harder to correct the error but can't if clamped. This might cause a current fault. Or when the clamp is removed the motor might react violently. I don't see any point in clamping the motor. Use a C program to enable the amplifier as soon as the KFLOP Axis is enabled.